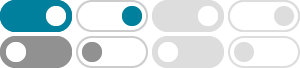
Proportional–integral–derivative controller - Wikipedia
The proportional, integral, and differential terms of the two controllers will be very different. The outer PID controller has a long time constant – all the water in the tank needs to heat up or cool down. The inner loop responds much more quickly.
The PID Controller & Theory Explained - NI - National Instruments
Mar 7, 2025 · As the name suggests, PID algorithm consists of three basic coefficients; proportional, integral and derivative which are varied to get optimal response. Closed loop systems, the theory of classical PID and the effects of tuning a closed loop control system are discussed in this paper.
Choosing a proper sampling time for a PID controller
Nov 28, 2015 · As Majenko's comment mentions, figure out what response time you want for your controller, then choose an appropriate sampling frequency that is say 10 times the desired frequency (so if you want 0.1 s response time, then use 100 Hz). $\endgroup$
How to Tune a PID Controller
The goal of tuning the integral value, is to achieve an adequate controller response or reaction time (after the initial response from the proportional is set). If the controller starts to oscillate, or become unstable, adjust the I value in the opposite direction until …
9.2: P, I, D, PI, PD, and PID control - Engineering LibreTexts
Mar 11, 2023 · Although the response time for PI-control is faster than I-only control, it is still up to 50% slower than P-only control. Therefore, in order to increase response time, PI control is often combined with D-only control.
PID loop tuning parameters and control fundamentals
Mar 28, 2023 · If the loop has a response time of several seconds up to about 30 seconds, choose a PI or PID controller. For slow loops with a response time of more than 30 seconds, using a PID controller is recommended.
Transfer function of PID controller is estimated using Z-N [1], [2], [6] and Routh’s Stability criteria [1], [2], [6]. The time response analysis is carried out to calculate response parameters, frequency response and Stability Analysis is carried out theoretically and by simulation.
Z-N rule enables tuning if a model and a computer are both unavailable, only the controller and the plant are. will keep growing while the control is constant. This results in a heavy. Ok, we have a controller that works for a nominal model. Why would it ever would work for real system?
estimation of minimum response time of a PID controlled system
Sep 23, 2018 · If you're aiming to implement a PID loop that gives you a faster stable step response than 60 msec, you should: 1. not be using a USB device due to the extra latency of the bus 2. use a device with higher resolution (& probably accuracy too) AI and AO
What is the Best PID Execution Time? - Control Global
Feb 22, 2012 · What is the Best PID Execution Time? An execution time that is too slow can degrade control loop performance. An execution time too fast can unnecessarily increase the loading in the distributed control system (DCS) or programmable logic controller (PLC).