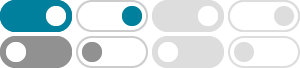
Gear Pump - an overview | ScienceDirect Topics
Mar 3, 2012 · The pump has to be heated to prevent polymer from solidifying in the gear pump during a process upset and process start-up. In normal operation, shear heat is generated by the rotating gears, minimizing the heat required. Unlike an extruder, the gear pump has no external air or water cooling to remove excess heat.
Design and Manufacture of Miniature Hydraulic Gear Pump
Jan 1, 2018 · Gear Pump A basic gear pump consists of a set of meshed gears, a case or housing to enclose the gears, and two cover plates that covers the ends of the gears. Each gear is mounted on shaft which is supported on bearings in the end covers. The drive shaft is coupled to the drive motor. The inlet and delivery ports are provided.
Gear pump for low power output ORC – an efficiency analysis
Sep 1, 2017 · Gear pump efficiency and losses A hydraulic work delivered by a pump can be in practical situations defined according to the Eq. (1). Mechanical input power can be calculated based on the rotational speed of the pump and torque on the shaft (see Eq. (2)). Isentropic efficiency of a pump is defined by Eq.
External Gear - an overview | ScienceDirect Topics
The internal gear pump is a reliable, inexpensive pump. The main disadvantage involves excessive backpressure or handling fluids that contain solids. Small gear pumps are limited to a backpressure of 100 psi (689 kPa) and require a pressure relief valve on the discharge side. Since small clearances exist, the manufacturer should always be ...
An advanced pressure pulsation model for external gear pump
Mar 15, 2023 · External gear pumps are more prevalent pumping components. The most common configuration uses a pair of meshing gears, which are supported by a pair of floating bearing blocks acting as seals for the lateral ends. The gear pump structure studied in this paper is shown in Fig. 1A. Relatively, the working principle of external gear pump is very ...
Elastodynamic analysis of a gear pump. Part I: Pressure distribution ...
Oct 1, 2010 · This section presents some simulation results about the gear SEP, the pressure distribution and the pressure forces and torques, concerning a pump with twin gears of 12 teeth, module of 1.15 mm, pressure angle in working condition of 27.727° and relief groove dimension of 2.9 mm; other pump parameters are reported in Table 1.
Non-stationary CFD Simulation of a Gear Pump - ScienceDirect
Jan 1, 2017 · The discharge part is ideally sealed. In the model we created individual zones for each material used and named the surfaces respective thereof. The figure shows the surface mesh. Fig. 2. a) Suction side of the pump (volumes with gear tolerance against the housing are marked ) b) Pump pressure side (ideally sealed gear against the housing).
Analysis of continuous-contact helical gear pumps through …
Sep 1, 2018 · For a gear pump, all the geometric features are periodic functions of the gear rotation angle ϕ, with a period of 2 π. In this paper, without further mentioning, the zero rotation angle ( ϕ = 0 ° ) corresponds to the position at which the driver TSV has the minimum volume (i.e. the sealing surface of the driver tooth-space is located at the ...
Experimental analysis of the flow dynamics in the suction chamber …
Feb 1, 2011 · The external gear pump that is used in this study has two identical cogwheels with eleven teeth each. The diameter of the gear is 53.6 mm and the depth is 36 mm. The theoretical volumetric capacity of this model is C ν =4.4×10 −5 m 3 /rev thus the flow rate in m 3 /s is Q = C v ω /2 π , where ω is the rotational velocity in rad/s.
Choosing the right gear pump applications - ScienceDirect
Aug 1, 1999 · Gear pump problems and solutions The following are a range of commonly encountered problems in gear pump operation, and some possible causes: Excess noise Entrained gas Inlet piping too small Misalignment Vibration in the relief valve Incorrect rotation Zero flow Check to see if the pump has primed.