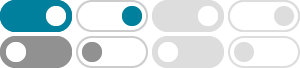
building a rig bed vs using your pickup bed
Apr 11, 2009 · A carefully built skid will be a fair bit lighter than a complete deck. That is why I changed the first rig from a deck to a p/u box skid, because I went from a 700lb welder to a …
Any built a removable teeth bar for a skid steer?
Most of the ones I have seen are made with the teeth welded to a bar, but the bottom of the tooth hooks over the cutting edge. Some make a vee out of steel to hook over the cutting edge and …
bobcat (skid loader bucket) - Miller Welding Discussion Forums
bobcat(skid loader bucket) Thanks MMW....boss decided he wanted me to fill the worn out areas in and just leave it go...got partially done with one side and it looked like crap...plus the 1/8 …
mini excavator weld - Miller Welding Discussion Forums
i talked with a fella that i used to work with in the quarries. if there was ever anything difficult to weld, jack did it. he said that if you gouge the cracks down to almost all the way through with a …
My skid - Miller Welding Discussion Forums
Mar 13, 2007 · This is the first skid I’ve made, so any criticism or suggestions would be greatly appreciated. I have already got one alteration with the tool boxes suggested by Piper Dan to …
Welding steel cable - Miller Welding Discussion Forums
Bobcat 250, MM 210, Syncrowave 180, Spectrum 375 Cat 242B Skid Steer, Challenger (Cat/Agco) MT275 1 Thessalonians 4:11-12
Crack On 1845 Case Skidsteer - Miller Welding Discussion Forums
Oct 18, 2005 · Repaired a crack today on this skidsteer behind p-side rear tire on bottom corner just under the axle spider assy.about 12" long and there is hydralic fluid inside this it seems to …
Replacing/repairing loader bucket - Miller Welding Discussion …
If there are just some thin spots at the back edge you could cut them out and patch it in.If the entire back edge is thin it may be time to replace the bottom.I would cut the perimeter and …
Fixing shanks on an Excavator Bucket? Hardfacing as well
Apr 8, 2007 · Gouge the old ones off, preheat the plate to 300 -375 degrees F, and weld the new ones on. Don't let the inter-pass temp drop below 250 deg F or go above 450. Allow the …
Duty Cycle - Miller Welding Discussion Forums
If it is 2:10 on 200 amps duty cycle, then that means weld for 2 minutes of every 10 minutes at 200 amps. So it needs approximately 8 minutes of "cool down time." The duty cycle is based …