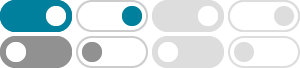
Accurately Measure Shear Droop on Cut Surfaces
Shear droop is a phenomenon that occurs on the surface of a product that was machined by shearing. When the machined material is cut using a punch and die, the material is pulled by the tensile force produced on the cut surface, producing a smooth surface. This smooth surface is known as droop.
Analysis of Shear Droop on Cut Surface of High-Tensile-Strength …
The shear droop is associated with the initial compression by and the subsequent clearance of the punches and dies. Results are obtained for various clearances and initial compressions in the fine-blanking process for high-strength steel, and the …
Investigation of shear droop formation around convex portions …
Jan 1, 2018 · A large shear droop generated in the convex portions of blanked components leads to functional problems, such as a decrease in the effective thickness of gear parts. In this study, the cause of this issue was investigated by comparing half-blanked workpieces with circular and rhombic profiles.
Causes of Pressing Defects (Burrs, Dents) and Observation of …
Shear droop: Smooth surface caused by the surface of the material being pulled. Sheared surface: Glossy surface with vertical stripes. There are subtle scratches caused by the punch cutting during shearing and friction between the deposited metal and the material.
Analysis of Shear Droop on Cut Surface of High-Tensile-Strength …
The shear droop is associated with the initial compression by and the subsequent clearance of the punches and dies. Results are obtained for various clearances and initial compressions in the fine-blanking process for high-strength steel, and the …
Press Dies Tutorial | Technical Tutorial - MISUMI
In common punching operations, the cut surface is formed in the material in the sequence of droop → shear cross-section → fracture cross-section → burr, as shown in Fig. 1.
Review of Shearing Processes of High Strength Steel Sheets
Jun 7, 2020 · Shearing processes of high strength steel sheets increasingly applied to lightweight automobile parts were reviewed. With the increase in strength of the high strength steel sheets, shearing operations become hard.
In this study, we investigated stability of the sheared surface length of the cross section in micro-pierced holes. The inner diameter of the holes and maximum piercing forces were measured in order to evaluate the effect of the grain size in the micropiercing process.
Analysis of Shear Droop on Cut Surface of High-Tensile
Mar 1, 2011 · In the present calculations, an adaptive remeshing technique for FEM is used to create fine sheared surfaces. The shear droop is associated with the initial compression by and the subsequent...
Sheet thickness vs droop/die-roll. | Download Scientific Diagram
A large shear droop generated in the convex portions of blanked components leads to functional problems, such as a decrease in the effective thickness of gear parts.