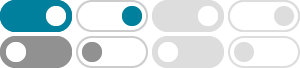
While the DeltaVTM PID function block ofers all of the functionality one would expect in a modern DCS such as series and standard execution forms, setpoint filtering, and bumpless tuning entry, DeltaV also provides advanced functionality to further improve control performance using PID.
the DeltaV PID and related function blocks. Discuss some common PID function block parameters where the default values can cause poor control. Provide examples of the use of these features. Note –“BOL” is DeltaV Books on Line (the embedded, electronic DeltaV documentation)
Dec 22, 2014 · PID stands for Proportional, Integral, Derivative. PID control is widely applied to mechanical equipment, pneumatic equipment, and electronic equipment. After all parameters are set, the instruction PID can be executed, and the result will be stored in D. D has to be an unretentive data register.
Interesting and Useful Features of the DeltaV PID, Ratio
Sep 29, 2010 · The document discusses several useful features of the DeltaV PID controller including PID form, structure, integral dead band, set point filtering and limits, cascade features, gain scheduling, non-linear gain, output characterization, anti …
Tips When Using DeltaV PID Control - Emerson Automation …
Oct 16, 2009 · DeltaV Books Online describes the input and output: BKCAL_IN is the analog input value and status from a downstream block’s BKCAL_OUT output that is used by a block for bumpless transfer. This connection is necessary if the …
DeltaV PID behavior query - Emerson Exchange 365
The proportional "kick" you saw makes sense based on the high Gain in your PID tuning (and assuming 0-100% scaling on PV and OUT). If you are using PI on Error, D on PV (the default and most common form in DeltaV), then your PID algorithm is working with an error of (SP - PV = 9 - …
Advanced Control & Analytics | Emerson US
4 days ago · DeltaV InSight is an integrated application to monitor, analyze, diagnose, report, and improve control loop performance. Continuously adjusts PID tuning for optimal control as process conditions change. Addresses single input/output control problems with a fuzzy logic control block as easy to implement as a PID block.
DeltaV PID options and parameters can: –Provide maximum disturbance rejection –Minimize setpoint overshoot and rise time –Eliminate limit cycles –Reduce valve maintenance –Coordinate loops for consistency and minimal interactions –Increase process efficiency –Increase feed rates –Protect equipment –Enable wireless control
Getting the Converted PID Values Right - Emerson Automation …
Feb 1, 2013 · The Provox PID controller users the Series form of PID, with PI action on error, D action on PV. The DeltaV PID controller is selectable between Series and Standard forms —but defaults to the Standard PID algorithm.
DeltaV Adapt continuously adjusts PID tuning for optimal control as process conditions change. In addition to calculating new tuning, DeltaV Adapt also remembers the best tuning from the last time it was controlling in the same operating region. And best of all, DeltaV Adapt can be applied to any PID loop in the control system – without
- Some results have been removed