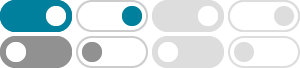
LM6 Aluminium Alloy: Properties, Applications, and Advantages
Sep 16, 2023 · Discover the versatile LM6 Aluminium Alloy: Explore its chemical properties, applications across industries, and the numerous advantages it offers. Learn why LM6 is a …
Melting Point of Aluminum Alloys - Table - Matmake
The melting point of aluminum alloys is typically between 460 - 670 °C (860 - 1240 °F). The tables below provide a comprehensive list of melting points for common aluminum alloys at one …
process is the treatment of the melt with strontium as an aluminium-silicon-strontium hardener. A more persistent state of modification is achieved by this method. HEAT TREATMENT Ductility …
Technical Data - aluminiumcastingseurope.co.uk
LM6 is used in many ‘marine castings’ water cooled manifolds and water jackets, motor vehicle and road transport fittings, intricate and thin section ccastings and for very large Aluminium …
workability of aluminum alloys are affected by porosity formation due to gas entrapment in the melting practices. Of the many casting techniques that are available, squeeze casting has …
LM6 (Aluminium) was melted at 720°C in the Induction furnace. Preheating of reinforcement (Fly Ash at 350°C, silicon carbide at 350°C) was done for one hour to remove moisture and gases …
In this study, the metal–matrix composites of an aluminum–silicon based alloy (LM6) with Lead oxide glass particles with % addition of 2.5%, 5%, 7.5%, and 10% were produced using a sand …
Micro structures of Al LM6 with melting temperature of 725 0 C.
The main purpose of this study was to investigate the silicon (Si) particles distribution of LM6 Aluminum Casting Alloy (Al LM6) cylinder produced by centrifugal casting method.
Mechanical properties of the as-cast quartz particulate reinforced LM6 …
May 26, 2008 · LM6 alloy is actually an eutectic alloy having the lowest melting point that can be seen from the Al–Si phase diagram. The main composition of LM6 is about 85.95% of …
(PDF) Effect of Pouring Temperature and Melt Treatment on ...
Jun 30, 2011 · Analysis on microstructure, eutectic silicon spacing and porosity percentage were conducted to determine the effect of both parameters. The results show that pouring …
- Some results have been removed